Mehr Flexibilität und Sicherheit für die Industrie
FAU treibt Erforschung mechanischer Fügeverbindungen und additiver Fertigung voran
Mit der Optimierung und Standardisierung mechanischer Fügeverbindungen beschäftigt sich ab Juli 2019 ein neuer Sonderforschungsbereich (SFB) an der FAU: Im SFB/TR 285 „Methodenentwicklung zur mechanischen Fügbarkeit in wandlungsfähigen Prozessketten“ sollen übergreifende Lösungen für die Verbindung von Halbzeugen, zum Beispiel Rohren und Blechen, vor allem für den Fahrzeugbau entwickelt werden. Bewilligt wurde auch die Verlängerung des SFB 814 „Additive Fertigung“, an dem neun Lehrstühle der Technischen Fakultät beteiligt sind. Ziel der dritten Förderphase ist es, den 3D-Druck von Bauteilen aus Kunststoff und Metall zur industriellen Anwendung zu bringen. Beide SFBs sollen einen wichtigen Beitrag dazu leisten, Bauteile und Produktionsprozesse zu optimieren, Fertigungszeiten zu verkürzen und eine höhere Planungssicherheit in der Industrie zu schaffen.
Universalbaukasten für mechanische Fügeverfahren
Komplexe Produkte, beispielsweise eine Automobilkarosserie, bestehen aus vielen Einzelteilen. Einige davon werden zunächst als sogenannte Halbzeuge, etwa vorgeformte Bleche, produziert und bei der Montage zusammengefügt. Das kann durch Schrauben, Nieten und Schweißen geschehen, aber auch durch Kleben, Clinchen oder Pinnen. Mit den steigenden Anforderungen an den Leichtbau und den Einsatz von Verbundwerkstoffen wachsen auch die Ansprüche an die Fügetechnologien.
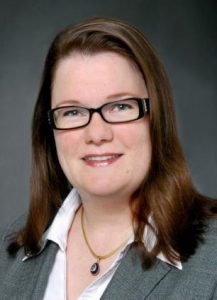
Im Laufe der Zeit hat sich eine Vielzahl individueller Lösungen entwickelt, die kaum auf andere Produkte übertragbar sind und auch bei geringfügigen Modifikationen aufwändig in die Prozesskette integriert werden müssen. „Eine Verringerung der Blechstärke, der Einsatz eines anderen Materials oder eine veränderte Form des Produktes kann zur Folge haben, dass neue Werkzeuge benötigt werden“, sagt Prof. Dr. Marion Merklein vom Lehrstuhl für Fertigungstechnologie (LFT). „Das benötigt viel Zeit, ist sehr kostenintensiv und verbraucht unnötig viele Ressourcen.“
Gemeinsam mit Forschenden der Uni Paderborn und der TU Dresden arbeitet die FAU im neuen SFB/TR 285 deshalb an universellen Lösungen, die einfach an veränderte Produktionsbedingungen angepasst und flexibel in die Prozesskette eingebunden werden können – einer Art Baukastensystem für Fügeverbindungen. In den Teilprojekten werden die unterschiedlichen Fügemethoden hinsichtlich Materialeignung und Verbindungssicherheit analysiert und optimiert. Das LFT und der Lehrstuhl für Kunststofftechnik (LKT) konzentrieren sich beispielsweise auf Pins, die verstärkte Kunststoffe durchdringen, ohne deren Fasern zu beschädigen und das Material dadurch zu schwächen.
Für die erste Förderperiode der insgesamt 16 Teilprojekte stellt die Deutsche Forschungsgemeinschaft (DFG) rund zehn Millionen Euro bereit, knapp drei Millionen Euro davon entfallen auf die FAU.
Leichte und stabile Bauteile aus dem 3D-Drucker
Ebenfalls von größtem Nutzen für den Bereich Automotive – aber auch für andere Industriezweige – ist die additive Fertigung. Nach dem Prinzip des 3D-Drucks werden Bauteile aus einem Pulverbett Schicht für Schicht aufgebaut. Ein Elektronenstrahl oder ein Laser bringen das Pulver punktgenau zum Schmelzen und formen geometrisch komplexe, leichte und zugleich hochstabile Konstruktionen aus Kunststoff oder Metall, die mit herkömmlichen abtragenden oder umformenden Verfahren nicht realisiert werden können.
Mit der additiven Fertigung lassen sich beliebige Formen in beliebigen Stückzahlen ohne spezielle Werkzeuge herstellen. Das eröffnet einerseits ein großes Spektrum an Anwendungsmöglichkeiten und senkt zugleich das Investitionsrisiko für Unternehmen. Besondere Gitterstrukturen bringen nicht nur neue Impulse für den Leichtbau, sie können auch die Dämpfungseigenschaften eines Produktes regulieren oder in Filtertechnologien eingesetzt werden. Außerdem wird es möglich, die Zahl der Einzelteile zu reduzieren.
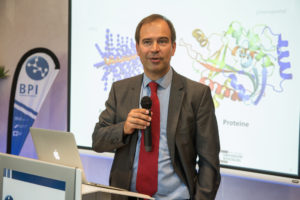
Um die additive Fertigung für den Einsatz in der Industrie fit zu machen, forschen neun Lehrstühle der FAU sowie das Bayerische Laserzentrum (blz) im SFB 814, der nun in die dritte Förderphase geht. „In der ersten Projektphase haben wir ein grundlegendes Verständnis dieses neuartigen Verfahrens entwickelt, in Phase zwei konnten wir die Technologie optimieren und einzelne Prozessschritte simulieren“, sagt Prof. Dr. Dietmar Drummer, Inhaber des Lehrstuhls für Kunststofftechnik (LKT) und Sprecher des Sonderforschungsbereichs. „Die dritte Phase dient nun dazu, die Technologie in die Produktion zu bringen.“ Dafür wollen die FAU-Forschenden zum Beispiel verbesserte Pulver herstellen, die Fertigungszeiten verkürzen und die Gestaltung der Bauteile optimieren. Zudem erarbeiten sie neue Methoden, mehrere Materialien in demselben Bauteil verarbeiten zu können.
Der SFB 814 wird von der DFG mit gut elf Millionen Euro gefördert.
Weitere Informationen:
Prof. Dr.-Ing. habil. Marion Merklein
Tel.: 09131/85-27140
marion.merklein@fau.de
Prof. Dr.-Ing. Dietmar Drummer
Tel.: 09131/85-29700
drummer@lkt.uni-erlangen.de