„Wir wollen die energieautarke Fabrik entwickeln“
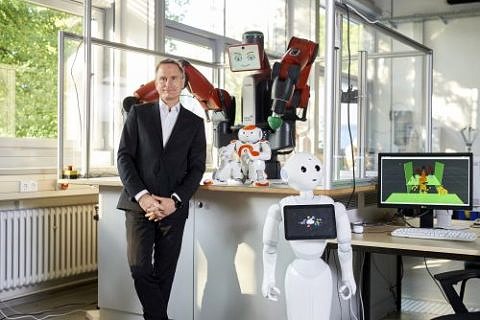
Prof. Dr. Jörg Franke im Interview zum Projekt Green Factory Bavaria
Vor sieben Jahren ist das Projekt Green Factory Bavaria gestartet. Zwölf Forschungseinrichtungen und über einhundert Unternehmen verfolgten gemeinsam das ehrgeizige Ziel, den Ressourcenverbrauch in der Produktion zu minimieren. Prof. Dr. Jörg Franke, Inhaber des Lehrstuhls für Fertigungsautomatisierung und Produktionssystematik (FAPS) an der FAU, hat das Verbundprojekt koordiniert. Wir haben ihn zu den wichtigsten Ergebnissen der Green Factory Bavaria befragt.
Prof. Franke, 2013 ist das Verbundprojekt Green Factory Bavaria gestartet – mit welchem Ziel?
Die Beschlüsse der Bunderegierung für eine regenerative Energieversorgung und zum Ausstieg aus der Kernenergie, der die Abschaltung der verbliebenen vier bayerischen Kernkraftwerke bis 2022 zur Folge hat, stellt uns vor gewaltige Herausforderungen. Insbesondere die Industrie ist gefordert, denn fast die Hälfte der elektrischen Energie wird durch die verarbeitende Wirtschaft verbraucht. Die Einsparungspotenziale sind immens – sie liegen bei bis zu 30 Prozent. Neben dem Beitrag zur Energiewende wird die Schonung von Ressourcen für die Unternehmen auch zum strategischen Wettbewerbsfaktor, weil Kunden, Mitarbeiter und die Gesellschaft eine wachsende Sensibilität für nachhaltiges Wirtschaften entwickeln. Die Green Factory Bavaria ist ins Leben gerufen worden, um bayerische Unternehmen bei der Senkung ihres Ressourcenverbrauches zu unterstützen und perspektivisch die energieautarke Fabrik zu entwickeln.
Mit welcher Strategie sollte dieses Ziel erreicht werden?
Wir haben zwei Hauptstoßrichtungen verfolgt: erstens den Transfer von der angewandten Forschung in die Industrie und zweitens die Organisation des Erfahrungsaustauschs zwischen den Unternehmen. Zehn Hochschulen und zwei Fraunhofer-Institute haben mit über einhundert Unternehmen aus ganz Bayern gemeinsam technische Lösungen und methodische Vorgehensweisen zur Reduzierung des Ressourcenverbrauchs entwickelt. Sogenannte Green Factories wurden als Demonstrations-, Lern- und Forschungsplattformen einer energieeffizienten Produktion auf- und ausgebaut. An jedem Standort wurden spezifische Technologieschwerpunkte gesetzt und die Ergebnisse anderen Unternehmen zugänglich gemacht.
Stellschrauben zur Energieeinsparung gibt es viele. Womit haben sich die Projekte beschäftigt?
Im Rahmen der Green Factory Bavaria wurden rund 80 Einzelprojekte gestartet. Das Spektrum ist unglaublich breit: Einige Teilvorhaben zielten auf das Produktionsmanagement, auf eine optimierte Maschinenbelegung und -wartung zur Vermeidung von Leerlaufphasen und Ausfallzeiten, auf kürzere Wege für Transportfahrzeuge und Roboter oder auf den Wegfall redundanter IT-Strukturen. Andere Projektgruppen arbeiteten daran, die Eigenschaften von Materialien und Verbindungen zu verbessern – glattere und härtere Oberflächen zur Reduzierung von Reibungsverlusten etwa, robustere Schaltverbindungen, bei denen auf energieintensive Wärme- und Kälteschockprüfungen verzichtet werden kann, Formgebungs- und Schweißverfahren, die sowohl Material als auch Energie einsparen. Uns war klar, dass die energieautarke Fabrik kein Ergebnis einzelner Patentlösungen sein wird.
Welche dieser Projekte waren besonders erfolgreich?
Ich würde das gesamte Vorhaben als großen Erfolg bezeichnen. 60 abgeschlossene Einzelprojekte mit insgesamt 61 finanzierten Vollzeitstellen, 23 Promotionen, 236 wissenschaftliche Publikationen und 324 wissenschaftliche Abschlussarbeiten – das sind schon beeindruckende Zahlen. Was die Energieeffizienz in den Betrieben angeht, gab zum Teil herausragende Ergebnisse: Im Projekt E|UROPA wurde durch die Optimierung der Elektroden beim Heißcrimpen bis zu 72 Prozent der benötigten Energie eingespart, 86 Prozent Einsparung gegenüber herkömmlichen Verfahren konnten zudem durch induktives Erwärmen erreicht werden. Im Projekt E|Vertech wurde ein Ultraschallschweißverfahren entwickelt, das den Energieverbrauch von Verbindungsprozessen im Elektromaschinenbau um 90 Prozent verringert. Das sind echte Highlights, und auch in fast allen übrigen Projekten konnten Energieeinsparpotentiale entdeckt und trotz der verhältnismäßig kurzen Dauer der Forschungsarbeiten bis zu einem gewissen Grad umgesetzt werden.
Gab es Bereiche, in denen sich Ihre Erwartungen nicht erfüllt haben?
Im Verlaufe der Projektarbeit stellte sich heraus, dass sowohl die Potenziale der Energieeinsparung als auch deren Umsetzung stark branchen- und prozessabhängig sind. So konnten beispielsweise bei der Umformtechnik ein Energieeinsparpotenzial von etwa 15 Prozent identifiziert und ein Drittel davon direkt umgesetzt werden. Im Bereich der Logistik zeigte sich ein Potenzial von etwa 80 Prozent, hiervon konnte ein Viertel unmittelbar gehoben werden. Als deutlich komplexer erwies sich die Verarbeitung von Kunststoff und Leichtbaumaterialien: Hier wurde zwar ein Potenzial von knapp 50 Prozent identifiziert, direkt umsetzbar waren allerdings nur zwei Prozent. Das macht deutlich, wie groß der Forschungsbedarf zur Entwicklung kreativer Maßnahmen noch ist.
Das Verbundprojekt ist bis Ende 2018 gefördert worden. Wie geht es jetzt weiter?
Durch die intensive Vernetzung der zwölf beteiligten Forschungseinrichtungen und über einhundert Industriepartner war die Green Factory Bavaria ein Katalysator für nachhaltige Forschungskooperationen in ganz Bayern. Auch die monetäre Beteiligung der Betriebe mit insgesamt über 10 Millionen Euro an den Projekten zeigte deutlich, welchen Stellenwert Nachhaltigkeit und Energieeffizienz in der Industrie inzwischen haben. Somit war schnell klar, dass das Projekt lediglich der Startschuss für weiterführende Forschung und Entwicklung sein würde. Seither haben wir an der FAU und insbesondere am FAPS zahlreiche neue Projekte initiiert und bereits umgesetzt, die direkt aus den Green-Factory-Projekten entstanden sind. Was uns ebenfalls sehr wichtig ist: Mit dem Verbundprojekt konnten wir nicht nur die Kooperation zwischen Wissenschaft und Industrie nachhaltig stärken, sondern auch zur Vernetzung der Industriepartner untereinander beitragen. In Zeiten zunehmender Globalisierung und Öffnung internationaler Märkte kann diese Bündelung industriellen Know-hows zum entscheidenden Wettbewerbsvorteil für bayerische Unternehmen werden.
Energie und Klima im Fokus
Auf dem Weltmarktführer Innovation Day am 8. September in der Heinrich-Lades-Halle dreht sich alles ums Thema Energie und Klima: Hier tauschen sich Unternehmensvertreterinnen und -vertreter zu Innovation im Energiesektor auf, Start-Ups aus der FAU präsentieren ihre Ideen zu Nachhaltigkeit.
Weitere Informationen
Prof. Dr. Jörg Franke
joerg.franke@faps.fau.de